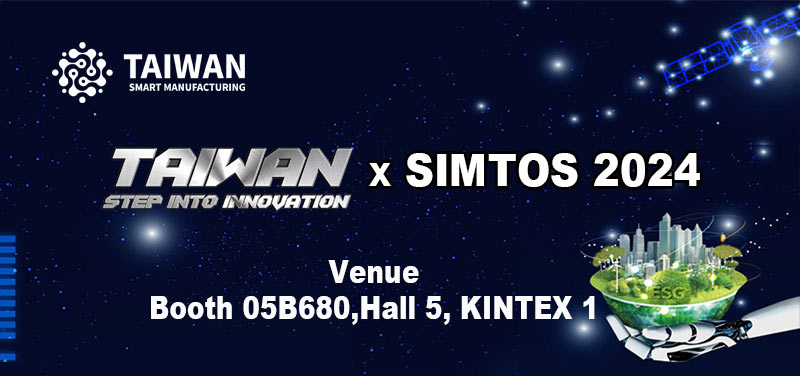 |
|
Unlocking Your Smart Manufacturing: SYNTEC's Total Solution Integrates Virtual and Real for Sustainable Efficiency |
Editor: Kim, Worldwide Services Co., Ltd. |
The Core Brain of Smart Manufacturing - Controller
Since its introduction at the Hanover Industrial Fair in 2011, Industry 4.0 has gradually become the method for manufacturers to optimize production processes. |
|
|
The goal of "smart manufacturing" is not only to automate production lines and reduce manpower but more importantly to achieve "virtual and real integration" through IIoT industrial Internet of Things, communication network, and cloud databases, establishing an automated management system for factories. In addition to real-time monitoring of equipment status, process adjustments, and increased capacity, manufacturing plants can also design quality traceability systems to meet the needs of overseas buyers. The precision can even be traced back to the production capacity of the factory at various time points, and the prerequisite for achieving these "smart manufacturing"? Installing the "controller" as the brain for machine tools.
|
While Taiwan's machine tool industry holds a significant share of global machinery sales, the vital "controller" technology has historically been dominated by foreign suppliers. However, with the recent backing of the Industrial Technology Research Institute, domestic controller manufacturers have made strides, carving out new avenues in the face of formidable competition from companies like Fanuc, Mitsubishi, Heidenhain, and Siemens.
|
SYNTEC Breaks Through with Openness and Inclusiveness
Founded in 1995, SYNTEC has adopted "openness" as its strategy from the beginning, allowing distributors or end customers to do custom software design according to their own needs, and their flagship product PC-Based CNC controller has strong inclusiveness, able to connect with motors from other manufacturers’ servo motors, and even including the high-precision built-in spindle motors. Today, as production lines move towards overall automation and connectivity, SYNTEC takes customer needs as the core strategy for development, providing a one-stop Total Solution.
|
SYNTEC's Product Manager, Hsu, pointed out, "Many Taiwanese manufacturers previously relied on Japanese controllers. While these controllers are dependable, their limited openness often results in similar products among machine manufacturers and leads to price competition." In response, SYNTEC developed a custom design software, the “Syntec IDE" to empower distributors and subsidiaries to tailor developments to customer requirements. Moreover, SYNTEC's headquarters swiftly addresses market needs by crafting specialized solutions, like the "high-gloss glass controller" for 3C glass grinding catering to a downstream supplier for smartphone manufacture. |
Putting Customer Needs at the Core
In recent years, the popularity of multitasking machines, such as machines combining turning and milling, turning and grinding, or turning and robotic arms, also greatly tests the technological development capabilities of controllers. SYNTEC has complete solutions to meet the needs of machine tool’s multi-tasking requests. In addition, SYNTEC launched the five-axis controller as early as in 2019, so they have built matured applications with using the related technologies such as multi-axis linkage, multi-axis & multi-task control, and multi-program applications, making them suitable for customers requiring high-precision complex surface machining. |
Providing More Than a Controller: A Complete Solutions Designer
In addition to the development of controllers with various specifications, SYNTEC has also developed complete servo solutions in recent years, including drivers, motors, encoders, etc., so it can adjust product functions according to the needs of end customers to achieve a one-stop Total Solution. |
A Little Less Energy Consumption, A Little More Production - The Sustainable Line Partner for Manufacturing
In early April, SYNTEC will join PMC to attend the Seoul International Manufacturing Technology Show (SIMTOS) in Korea, showcasing a complete set of solutions integrating controllers, drivers, motors, encoders and providing manufacturers with a more complete selection of smart production lines. Another focus from SYNTEC at the exhibition is their newly self-developed spindle motor solution, the "Disc Motor", which not only accelerates and decelerates within a short time, possessed high precision in the C-axis, but it is made with light weight and easy maintenance. Also, because it does not rely on belt drive, it can eliminate the problem of belt wear. "Chip-breaking cutting" and "smart grinding machines" can greatly reduce energy consumption, improve productivity, and have been the focus of attention in recent years. |
Facing sustainability issues, as global manufacturers strive towards goals of low carbon, low energy consumption, and high efficiency, SYNTEC is also prepared to become the green partner of manufacturers. Last month, SYNTEC won four awards in the "Energy Saving Label" evaluation held by the Taiwan Machine Tool and Accessories Builder’s Association. The four products are:
- Energy Monitoring Solution - Sensorhub Energy Management & Synfactory Intelligent Equipment Management
By installing Sensorhub for monitoring and managing energy consumption in processes, it helps factories achieve precise savings and improve on their production efficiency.
- Energy-saving Servo Tech.- Power-regenerating Combined Driver
Through innovative power-regenerating technology, the excess kinetic energy generated during the process is converted into "electric energy" through newly developed technology and sent back to the power source, allowing the motor to operate while regenerating electricity.
- Lathe Controller - Chip-breaking Cutting Energy-saving Technology
During machine cutting, the SYNTEC patented technology is used to fracture the chips generated by cutting, replacing the high energy-consuming and water-intensive high-pressure water pumps.
- Grinding Machine Controller - Intelligent Grinding Energy-saving Function
By accurately monitoring and sensing the wear of grinding wheels during processing, the risk of affecting product yield due to grinding wheel wear is reduced, and the number of grinding wheel replacements can also be reduced while improving the processing efficiency.
|
Integrating Virtual and Real in Factory, SYNTEC Lays Out Comprehensive Strategies
"SYNTEC has its own insights into the development of smart manufacturing. We are also preparing to join the ISO-14064-1 greenhouse gas inventory system in the second half of this year and actively developing factory automation solutions," explained SYNTEC Manager HSU. SYNTEC's one-stop Industry 4.0 solution connects IIoT industrial Internet of Things, communication network, and cloud databases, making the production efficiency, current status and capacity of machines visible. In addition, focusing on the development of mechanical arms and cloud system integration, the subsidiary LEANTEC, and the laser marking, cutting, and welding technology of "JUMBO Laser" will assist machine factories in moving towards low carbon and low pollution. The newly developed intelligent marking machine by JUMBO can also automatically engrave QR codes on workpieces, facilitating subsequent quality traceability for processors. In the wave of virtual and real integration applications, SYNTEC is ready for its customers. |
|
|
|
|
|